It’s no secret that having a healthy workforce is a benefit to both company managers and the bottom-line. Research shows healthy employees are more productive, have less absenteeism, and tend to be more engaged with the work they are doing. But with 47% of the US workforce being aging baby boomers and 69% of those over the age of 20 being considered overweight or obese, it is unlikely your supervisor will simply inherit a healthy workforce.
Instead, smart companies are investing in proactive, preventative measures to ensure their workforce is healthy and able to effectively complete their tasks. In our six-part series, Six Pitfalls to Avoid When Creating a World-Class Injury Prevention Program, we will examine common mistakes made when creating a prevention program and provide tips for how to avoid those pitfalls.
In part 1, we will examine one of the most common pitfalls we encounter when helping companies establish an injury prevention program – believing a program can design out all injury risks.
Why Can’t All Risk Be Designed Out?
When we began working with one of our pharmaceutical clients, we encountered this pitfall due to their highly regulated environment. In order to comply with federal and state regulations, this client had a procedure and policy for everything. One of their policies was a “zero-tolerance” policy, which meant they wanted to create a program where there were zero work place injuries. However, given that they employed humans, and not machines, we knew this was just not possible. Why? Humans fall, trip and bend in awkward motions; it is impossible to have zero risk no matter how great the training, equipment or protocols.
For example, with this client, they stored drugs on shelves that were approximately 12 feet high. To reach those drugs, employees were required to climb a ladder. Anytime there is a ladder involved in a task, there is going to be some risk. During our initial risk assessment, we discussed the option to remove the ladder from the task by putting in a scaffolding system, but the cost was prohibitive. This meant, that there was no way we could ever design that job function to have zero risk.
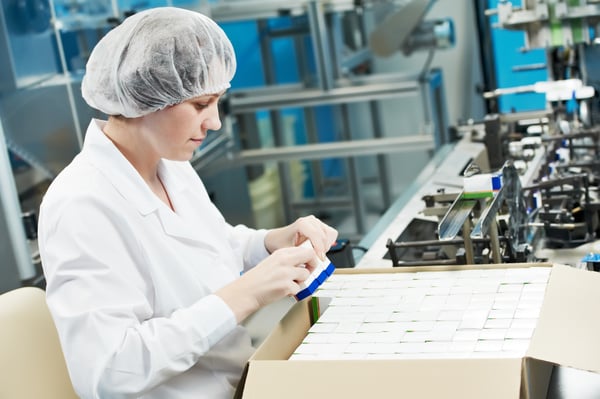
Humans Make Choices
After walking management through the tasks they were asking employees to complete, they understood that even with the most thorough procedures and well-designed injury prevention plan, all risk could never be designed out. Companies employ humans. Humans make choices. When designing an injury prevention program, we are not trying to design out all risk because we are not designing out all humans. Rather, we focus on building a culture of safety and educating employees on habit changes that can make a significant reduction in the risk of a work-related injury.
Learn More About Risk Assessment Consulting
While the human factor makes it impossible to design out all work-related injury risks, a comprehensive workplace assessment can assist management in identifying those risks and provide solutions to help reduce the chance of injury. Briotix offers onsite site evaluations that include a job hazard analysis and site safety audit with identification, documentation and remediation of workplace hazards. To learn more about our technical consulting services that will help you create a world-class musculoskeletal injury prevention plan, contact Briotix today. Give us a call or complete the online request form.