Turnover and hiring are major difficulties in every industry. The incredible investment of time, resources, and training for an experienced worker is a massive sum. Searching for capable workers to replace employees who have left takes time, money, and considerable skill, especially in an industry like construction where the skill differential between new hires and seasoned construction can be massive. When preventable injuries and claims become a major source of turnover in your company, it is time to make a change.
So, what can the industry do in 2023 to increase retention in their workforce?
Increasing Retention in Construction
Holding onto knowledgeable employees can be difficult but the benefit is exceptional. The Society for Human Resource Management has determined the cost of hiring a new employee in totality can equal three times an employee’s annual salary with 30 to 40% in hard cost while the rest is in soft costs.
Three practices you can put into place right now to improve retention are:
1. Breakdown communication barriers with on-site translators.
With the diverse backgrounds of many experienced construction workers, proper communication is key. Having employees on hand who speak the first language of all workers shows respect for them and their work. In the US, English and Spanish translators may be necessary on the job site, and in Canada, additional French translators can be useful.
2. Complete a compensation study to ensure compensation is aligned with industry standards.
Experienced employees should also be properly compensated. Moving experienced workers to leadership positions, assigning personalized projects suited to their skills, and letting them choose their teams can encourage them to stay at your company. Setting up specific incentive factors alongside normal promotions can be a great retention tool.
3. Improve the health and safety of your workforce by addressing preventable injuries.
In construction, the chance of musculoskeletal disorders is understandably high given the physicality of the work. The prevalence of MSDs was measured at 33.8% in a study on their rate of occurrence in the construction industry. While the risk of an MSD injury is higher, most MSD injuries are preventable with proper training and administrative controls.
One way to prevent these types of injuries is to begin training early in the career with a focused injury prevention and ergonomic program. When new hirers understand proper body mechanics and the ergonomics behind their work, there is not only a reduced risk of injuries, but workers also see the company demonstrating an increased investment in employee health and well-being which can signal that your company is a place to stay for the long term.
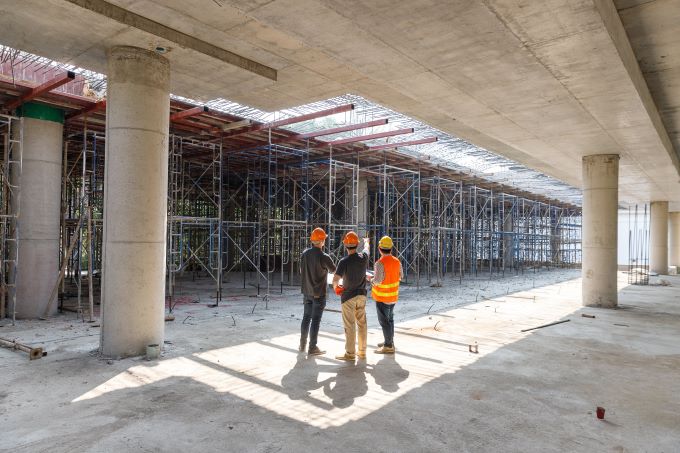
Establishing an Injury Prevention Program
An injury prevention program, with clear and specific goals, will enhance your retention and set up a healthy environment for new hires to thrive. So, what are those clear and specific goals?
The first step when creating or adopting an injury prevention program is to establish what you are attempting to gain from it. To do that, you have to understand what it can offer.
-
Generally, an injury prevention program is used to identify and then establish a pattern of behavior in the workplace that promotes a reduced risk of injury and employee well-being.
-
Specifically, an injury prevention program analyzes your workplace, from specific areas of concern to everyday tasks employees complete, to find and eliminate risk factors that increase the risk of injury. Using input from supervisors, employees, and management, injury prevention experts create solutions that improve productivity and well-being among employees.
The National Institute of Occupational Safety and Health (NIOSH) can give even more detail.
In construction, these risk factors could look like improper use of tools at workstations, a disregard for proper materials handling protocols, or failure to follow OSHA safety regulations. Each of these introduces the risk of discomfort in the workplace which can evolve into injuries and claims.
So, with these points in mind, what are some sample goals that could be established when looking for an injury prevention program?
-
A program that can be used in the projects my company most often works on.
-
With the vast amount of construction projects, it can be difficult to find the ergonomic solution that fits you. Whether you are doing short-term projects at a small location or large-scale projects on a single worksite for a long period, identifying a program that fits your needs is important in reducing MSD injuries.
-
A program employees, old and new, can incorporate into their workflow.
-
A program employees and supervisors actively support the program inside and outside the work environment.
-
A program that prevents discomforts, injuries, and claims common in your work.
-
Eliminating back injuries, shoulder discomforts, and other MSDs is crucial to building the healthiest workplace you can. An ergonomic program should address all these issues and ones specific to your work.
-
A program that reduces costs.
Establishing an Injury Prevention Program
The introduction of an injury prevention program is essential to a successful employee journey and increased employee retention. Implementing simple tips and tricks can be a good way to get started today.
Implement a daily stretching program. This encourages employees to keep their well-being in mind and can activate the muscle groups they will be using throughout the day. You can hand out these materials to new hires as well so they can stretch at home as well.
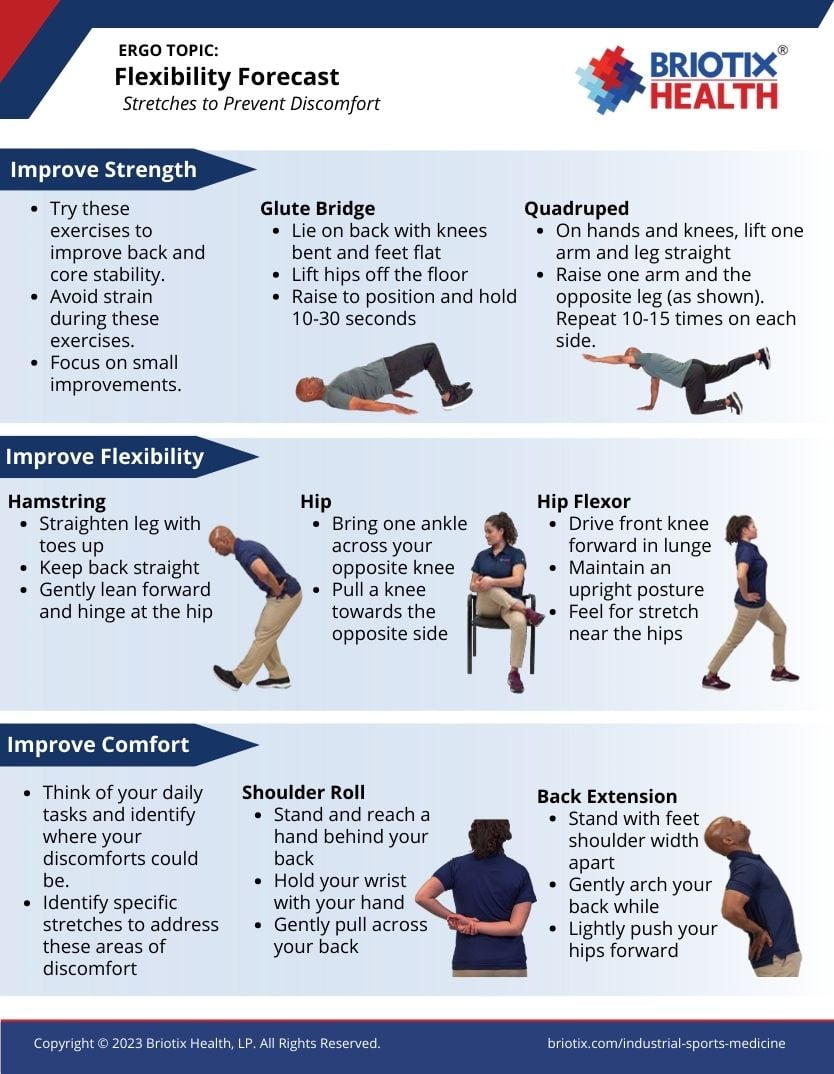
Dispose of malfunctioning or jury-rigged tools. Tools are designed specifically for use. Mishandling tools and other implements can lead to discomfort over time and eventual injury, costing more in claims than in replacing the tools. Don’t let new employees use these tools or they could develop bad habits over their career.
Check safety equipment. Educating employees on usage AND proper maintenance keeps them safer. Hoists, lifting belts, and other safety measures should be the responsibility of every employee who interacts with them.
The most important factor in employee retention and fostering new hires is showcasing that you understand their value. By developing a relationship and understanding what these employees bring to your business you increase morale and participation in safety and can significantly reduce costs.
If you are looking to enhance your ergonomic program with data-backed insights from experts, contact Briotix Health today. Our suite of services leads in injury prevention, overall cost savings, and employee satisfaction.